Thursday, June 28, 2007
IT RUNS! NO SMOKE!
So I took the engine apart, all the way down to the piston and rings, then reassembled the rings on the pistons, reassembled the engine, and started it up! TaDA!! It runs and no smoke!!
Have been busy doing some tuning. So far, I am upto about 8.5psi... and that will be my base boost level. It is already SOOOO powerful! I cant wait to goto 18! Its going to be just insane!!
Will take some pictures and also a video soon.. I wonder if I can post videos on these blogs??
Stay tuned, hopefuly with a dynosheet that reads 300whp+!
Sunday, June 3, 2007
Dont know what this is??
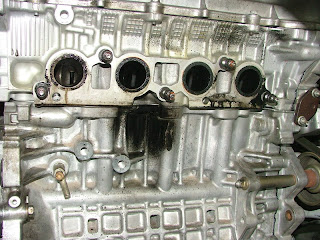
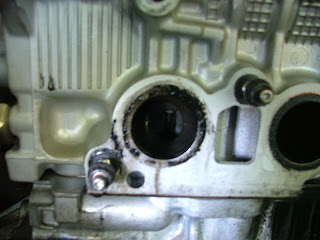
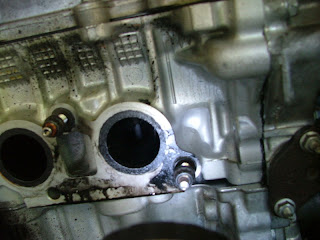

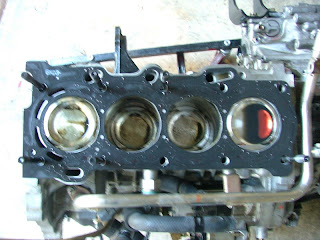
Tuesday, May 15, 2007
Good News!
The good news is that the manual conversion worked!! No manual harness needed, just a few wiring modifications to the starting circuit. Also, the shifter fork needs to be slightly modified somewhat so that the slave cylinder has got something on the end of the fork to push against (I welded a nut onto the end of the fork, cut the end bit of a stud off, and screwed the stud into the nut. The rod of the slave cylinder then pushes against the small bit of stud inside the nut. Works like a charm!
Anyway, on with the show!
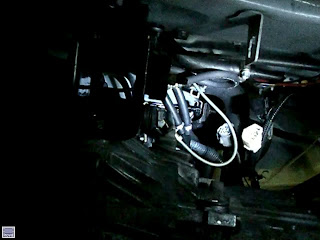
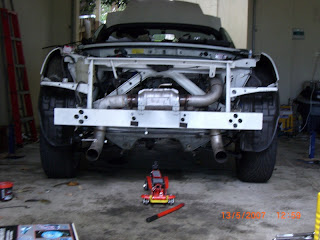
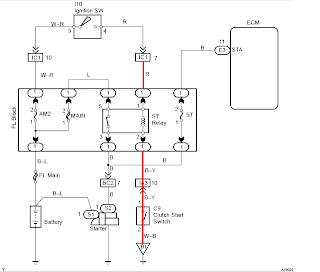
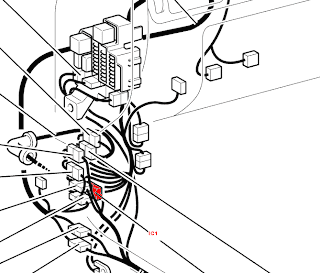
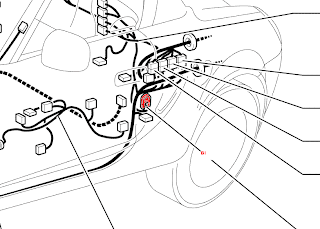
Saturday, May 5, 2007
Update!
Ok, so on with the picture show! :-)
Friday, March 9, 2007
Its a BENT ROD too!
Rods were easy enough to get out... Much easier than I thought... Remember from my previous post, the piston in cylinder number 1 never quite made it all the way to the top, and I couldnt understand why??
Well, this is why!! BENT Rod!! I couldnt believe that my engine was still running though! It turned over easily enough, and there were no combustion chamber leaks anywhere... This is very odd, considering that most bent rods would have caused major scoring of the cylinder walls and it would have been blow-by heaven! (blow-by is where the oil from the crank case gets into the combustion chamber because of either faulty rings, or too much clearance between the ring and the cylinder walls.
Upon closer inspection of the cyliner walls, I found a little notch at the base of cylinder number 1. This notch must have been made by the force of the bent rod stiking into the cylinder walls... This would have also caused some rather unsettling engine noise!
A closer look! I think I may be REALLY lucky here. Dont think I will need to sleeve this cylinder because the top two rings on the new WISECO pistons will never get as low as where the notch is, so I shouldnt have any sealing issues.... I think!
Saturday, March 3, 2007
The Engine Tick - I Found It!
A few discoveries...
So, this was what was causing the ticking noises from the head! It must have been the valves hitting the plastic on the way up... Also, did a careful examination of the cylinder bores and pistons... Everytime I did a compression test, one of the cylinders always came up a little lower then the others...
Now, have gotten to the stage where I can really do no more on the engine without the right tools. Will be calling a friend for access to his facilities! :-)
Also, still waiting for the last of the manual conversion parts to come in... the shifter shaft is still not here, nor are the clutch lines... *sigh*
Sunday, February 25, 2007
SMT Off!!
Anyway, onto the pics...
The black rubbery looking thing to the left of the realy long bolt is the clutch actuator arm.. more pictures below to explain its operation.
Ok, thats the latest... on the engine front, still waiting for speciality tools to arrive from the USA so I can get those head studs off!! Also need a special twist off socket for the one head stud which I rounded off when trying to undo with an Allen Key... moral of the story, dont use an Allen Key, use a proper 12 point (also know as double-hex, or triple-square), 10mm bit!!!